Matters needing attention in packing work on transport container route.
1. All cases are packed by manpower.
2. Use a fork-lift truck (forklift) to move into the box, and then use manpower for stacking.
3. All cases are packed by machinery, such as pallet (pallet) goods are stacked in the case by forklift trucks.
Among the three methods, the third method is the most ideal, with the highest loading and unloading rate and the least occurrence of cargo damage. However, even if all boxes are mechanically packed, if the characteristics and packaging conditions of the goods are ignored during loading, or due to improper operation and other reasons, accidents of cargo damage will often occur. Especially for containers loaded in inland areas, because the packer does not know the state of the container during sea transportation, the loading method usually does not meet the requirements of sea transportation, which causes cargo damage accidents. There are many such cases. The following briefly analyzes the matters that need to be paid attention to when packing work on the transport container.
Matters needing attention when doing packing work on transport container route:
1. When packing goods on a transport container route, under any circumstances, the weight of the goods in the box cannot exceed the maximum loading capacity of the container. The maximum loading weight of the container is obtained by subtracting the total weight of the container from the weight of the container. The maximum load weight. The total weight and dead weight are generally marked on the door of the container.
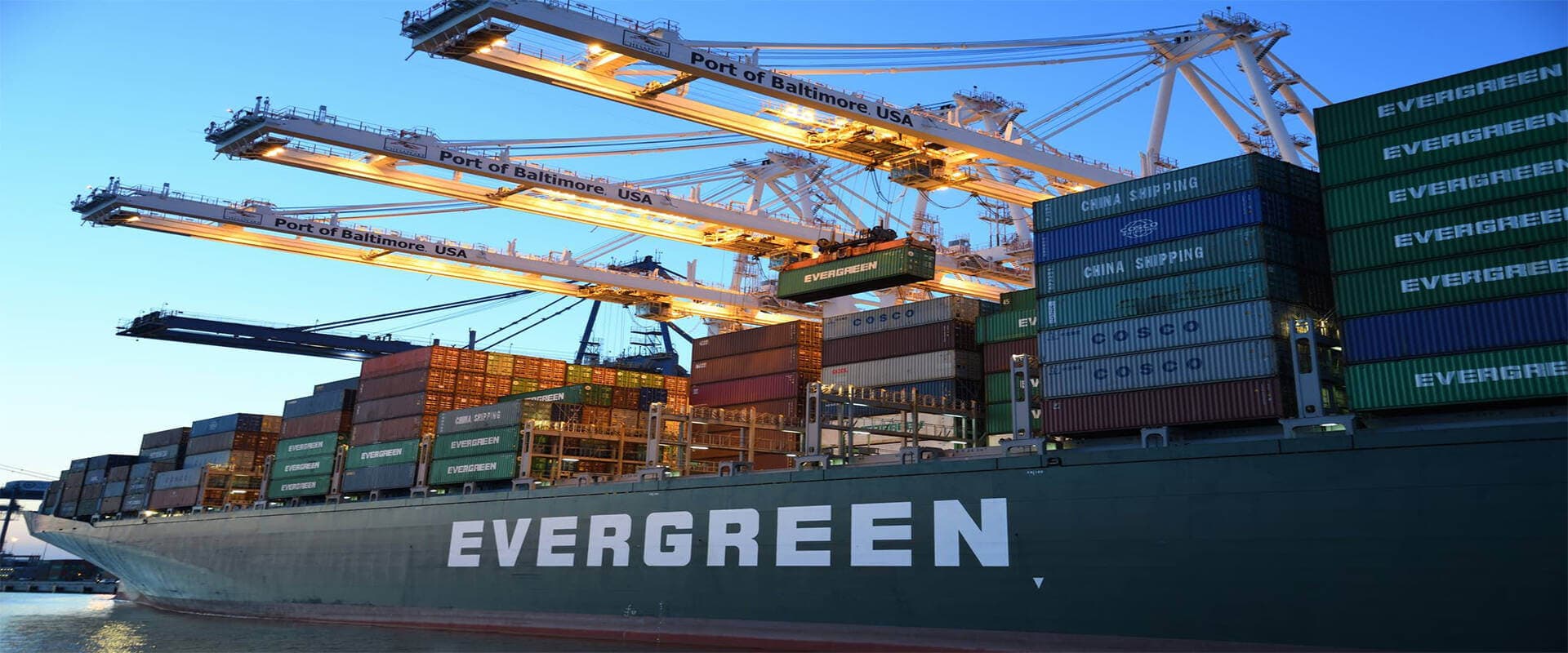
2. The unit weight of each container is certain, so when loading a kind of goods in the box, as long as the density of the goods is known, it can be judged whether it is heavy or light. The cargo whose density is greater than the unit weight of the box is heavy cargo, and the loaded cargo is calculated by weight. Conversely, if the density of the cargo is less than the unit weight of the box, it is light cargo, and the loaded cargo is calculated by volume. It is important to distinguish these two different situations in time to improve the efficiency of packing.
3. When loading on a transport container route, balance the load on the bottom of the container, and the load in the container cannot be biased to one end or one side. In particular, it is strictly forbidden that the center of gravity of the load is biased to one end.
4. To avoid concentrated load, for example, when loading heavy goods such as machinery and equipment, the bottom of the box should be covered with padding materials such as wooden boards to spread the load as much as possible. The average safety load per unit area on the bottom of a standard container is roughly as follows: a 20-foot container is 1330x9.8N/m, and a 40-foot container is 980x9.8N/m2.
5. When loading the goods by manpower, pay attention to whether there are loading and unloading signs such as "not upside down", "flat", "vertical", etc. on the package. To use loading tools correctly, hand hooks are forbidden to be used for bundles. The goods in the box should be neatly and tightly packed. Goods that are easy to be loosely bundled and packaged are fragile. Use padding or insert plywood between the goods to prevent the goods from moving in the box.
6. When loading pallet cargo on a transport container route, it is necessary to accurately grasp the internal dimensions of the container and the external dimensions of the cargo packaging, so as to facilitate the calculation of the number of loaded pieces, so as to achieve the purpose of minimizing abandonment and loading more cargo.
7. When using a forklift truck to load the box, it will be limited by the free lifting height of the machinery and the height of the mast. If conditions permit, the forklift can load two layers at a time, but there must be a certain gap between the top and bottom.